Introduction:
Work trucks are an essential component of many industries, serving as the backbone for transporting goods, equipment, and personnel to various job sites. Whether used in construction, landscaping, delivery services, or any other field requiring transportation of heavy loads, work trucks play a vital role in keeping businesses running smoothly. However, these vehicles are subjected to rigorous wear and tear due to their demanding work environments, making regular inspection and maintenance crucial to ensure their safe operation.
Work truck inspection is a systematic process of assessing the condition of the vehicle to identify any defects, damages, or malfunctions that could affect its performance, safety, or compliance with regulatory standards. By conducting thorough inspections on a regular basis, businesses can prevent accidents, reduce downtime, lower maintenance costs, and extend the lifespan of their work trucks. In this comprehensive guide, we will delve into the importance of work truck inspection, the key components to examine, best practices for conducting inspections, and how to develop an effective inspection program.
Importance of Work Truck Inspection:
Work truck inspection is a critical aspect of fleet management that directly impacts the safety of drivers, passengers, and other road users. Regular inspections help identify potential issues before they escalate into major problems, reducing the risk of accidents and ensuring compliance with safety regulations. By proactively addressing maintenance needs through inspections, businesses can prevent costly repairs, breakdowns, and downtime that can disrupt operations and impact profitability.
In addition to safety considerations, work truck inspection plays a key role in maintaining compliance with regulatory requirements. Government agencies, such as the Department of Transportation (DOT) in the United States, mandate specific inspection standards for commercial vehicles to ensure they meet minimum safety and operational criteria. Failing to comply with these regulations can result in fines, penalties, and even loss of operating licenses, putting businesses at risk of legal liabilities and reputational damage.
Furthermore, effective work truck inspection practices contribute to improved efficiency and productivity in fleet operations. Identifying and addressing maintenance issues promptly can help prevent unexpected breakdowns and delays, allowing businesses to maintain optimal performance levels and meet project deadlines. By keeping work trucks in top condition, companies can maximize their utilization, minimize fuel consumption, and enhance overall operational efficiency.
Key Components of Work Truck Inspection:
A comprehensive work truck inspection covers various components of the vehicle to ensure its safe and reliable operation. While the specific inspection checklist may vary depending on the type of work truck and industry requirements, there are several common areas that should be included in every inspection:
1. Exterior Inspection:
- Check for any signs of damage, such as dents, scratches, or rust.
- Inspect the lights, reflectors, and signals to ensure they are functioning properly.
- Examine the tires for wear, damage, and proper inflation.
- Verify the condition of the windshield, mirrors, and wiper blades.
- Inspect the body and chassis for structural integrity and signs of corrosion.
2. Engine and Mechanical Components:
- Check the engine oil level and condition.
- Inspect the coolant, brake fluid, power steering fluid, and other fluid levels.
- Examine the belts, hoses, and filters for wear and tear.
- Verify the battery condition and terminals.
- Test the brakes, including pads, rotors, calipers, and brake lines.
3. Electrical Systems:
- Check the battery voltage and charging system.
- Inspect the wiring, fuses, and connectors for damage or corrosion.
- Test the operation of lights, horn, wipers, and other electrical accessories.
- Verify the functionality of safety features, such as seat belts and airbags.
- Ensure the dashboard gauges and indicators are working correctly.
4. Interior Cabin:
- Inspect the condition of seats, upholstery, and flooring.
- Check the functionality of heating, ventilation, and air conditioning systems.
- Verify the operation of controls, switches, and instruments.
- Test the visibility through windows, mirrors, and cameras.
- Ensure the proper stowage of emergency equipment, tools, and supplies.
5. Cargo and Load Handling Equipment:
- Inspect the condition of the cargo area, including tie-down points and securing devices.
- Check the operation of hydraulic systems, lifts, cranes, and other load handling equipment.
- Verify the weight distribution and securement of loads.
- Ensure compliance with weight limits and load restrictions.
Best Practices for Conducting Work Truck Inspections:
To ensure the effectiveness of work truck inspections, businesses should follow best practices that promote thoroughness, consistency, and accountability in the inspection process. Here are some key practices to consider when conducting work truck inspections:
1. Establish an Inspection Schedule:
- Develop a routine inspection schedule based on the vehicle's usage, mileage, and operating conditions.
- Ensure that inspections are conducted at regular intervals, such as daily, weekly, or monthly, depending on the frequency of use.
- Document the inspection schedule and maintain records of completed inspections for tracking and compliance purposes.
2. Train Inspectors:
- Provide training to designated inspectors on proper inspection procedures, techniques, and safety protocols.
- Ensure inspectors are familiar with the specific components and systems of the work trucks they are inspecting.
- Encourage inspectors to stay updated on regulatory requirements and industry best practices related to work truck inspection.
3. Utilize Inspection Checklists:
- Develop comprehensive inspection checklists that cover all critical components and systems of the work truck.
- get redirected here based on the specific make, model, and configuration of the vehicle.
- Use digital inspection tools or mobile apps to streamline the inspection process and facilitate real-time reporting.
4. Conduct Pre-Trip Inspections:
- Require drivers to perform pre-trip inspections before operating the work truck.
- Encourage drivers to visually inspect the vehicle, check fluid levels, and test key systems before starting their journey.
- Empower drivers to report any issues or concerns identified during pre-trip inspections to maintenance personnel for prompt resolution.
5. Address Deficiencies Promptly:
- Prioritize the repair and maintenance of any deficiencies identified during inspections.
- Establish clear procedures for reporting and documenting inspection findings.
- Schedule timely repairs and follow-up inspections to ensure that identified issues are resolved effectively.
6. Monitor Inspection Compliance:
- Implement a system for monitoring inspection compliance and tracking inspection outcomes.
- Analyze inspection data to identify trends, recurring issues, and areas for improvement.
- Use inspection reports to inform maintenance schedules, budgeting decisions, and fleet management strategies.
Developing an Effective Work Truck Inspection Program:
Creating a comprehensive work truck inspection program requires careful planning, coordination, and commitment from all stakeholders involved in fleet management. By following a structured approach to developing an inspection program, businesses can optimize the safety, reliability, and performance of their work trucks. Here are key steps to consider when establishing an effective work truck inspection program:
1. Define Inspection Policies and Procedures:
- Establish clear policies and procedures for conducting work truck inspections, including roles and responsibilities of inspectors, drivers, and maintenance staff.
- Define the frequency, scope, and documentation requirements for inspections based on regulatory standards and industry best practices.
- Communicate inspection protocols to all relevant personnel and provide training as needed to ensure compliance.
2. Select Inspection Tools and Technologies:
- Evaluate available inspection tools, such as paper checklists, digital forms, or mobile apps, to determine the most suitable option for your fleet.
- Implement technology solutions that streamline the inspection process, improve data accuracy, and enhance reporting capabilities.
- Consider integrating inspection tools with fleet management systems to track inspection results, maintenance schedules, and compliance status.
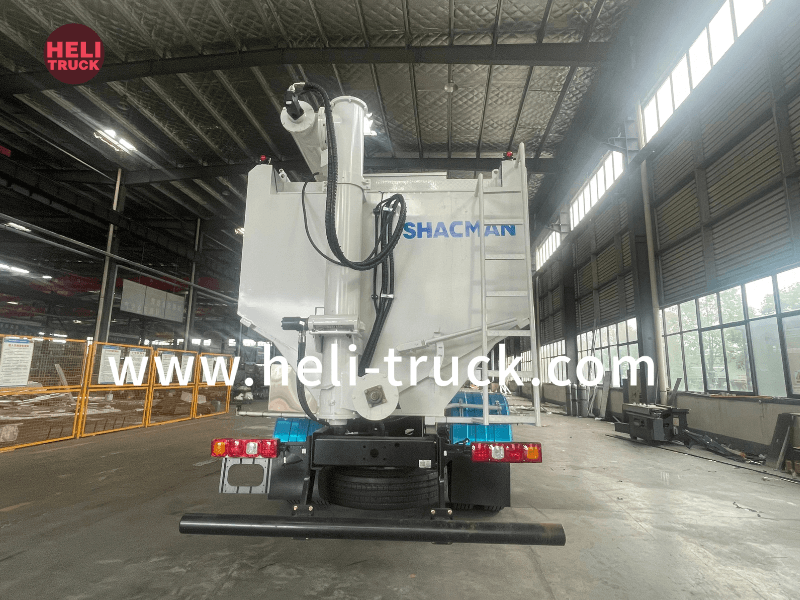
3. Establish Maintenance Procedures:
- Develop a proactive maintenance plan based on inspection findings and manufacturer recommendations.
- Schedule routine maintenance tasks, such as oil changes, tire rotations, and filter replacements, to keep work trucks in optimal condition.
- Coordinate maintenance activities with inspection schedules to ensure timely repairs and minimize downtime.
4. Monitor Performance Metrics:
- Define key performance indicators (KPIs) to measure the effectiveness of the work truck inspection program.
- Track metrics related to inspection completion rates, defect identification, repair turnaround times, and overall fleet reliability.
- Use performance data to identify areas of improvement, allocate resources efficiently, and demonstrate the program's impact on operational outcomes.
5. Implement Continuous Improvement Practices:
- Establish a feedback loop for collecting input from inspectors, drivers, and maintenance personnel on the inspection process.
- Encourage regular review and refinement of inspection checklists, procedures, and training materials based on feedback and lessons learned.
- Foster a culture of continuous improvement that emphasizes learning from past experiences and striving for excellence in work truck inspection practices.
Conclusion:
Work truck inspection is a fundamental aspect of fleet management that directly influences the safety, compliance, and efficiency of commercial vehicles. By prioritizing regular inspections, businesses can proactively identify and address maintenance issues, reduce the risk of accidents, and optimize the performance of their work trucks. Through the implementation of best practices, development of comprehensive inspection programs, and commitment to continuous improvement, organizations can ensure the long-term reliability and sustainability of their work truck fleets. By investing in work truck inspection as a core component of fleet management, businesses can safeguard their operations, protect their assets, and uphold their commitment to safety and excellence in transportation services.